福建哪里有連續(xù)式滲碳爐銷售
發(fā)布時間:2022-04-18 01:08:23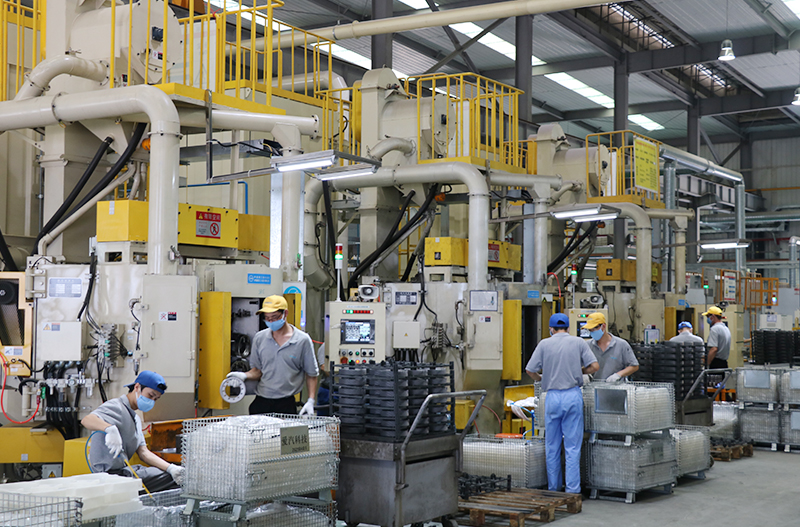
福建哪里有連續(xù)式滲碳爐銷售
如何提升升溫速度。熱處理生產線如今已經成為了工業(yè)熱加工中不可缺失的設備,盡管當前來講煤炭仍舊是主要產熱能源之一,但是由于污染嚴重,且對高溫空氣燃燒技術工藝的發(fā)展沒有比較好的促進作用,因此為實現進一步提升工業(yè)爐升溫速度,利用氣、油等固體燃料加以代替成為了如今的發(fā)展方向。為實現熱處理生產線能夠比較快的升溫且不會造成能源的大量流失,進一步完善開發(fā)并推廣高溫空氣的燃燒技術,也是增加未來熱處理設備向節(jié)能方向發(fā)展的前提。而在實現火焰溫度以及能效的基礎上,實現生產線中各設備爐膛溫度的平均分布也比較的重要,因此這也是未來提升升溫效率的研究方向。
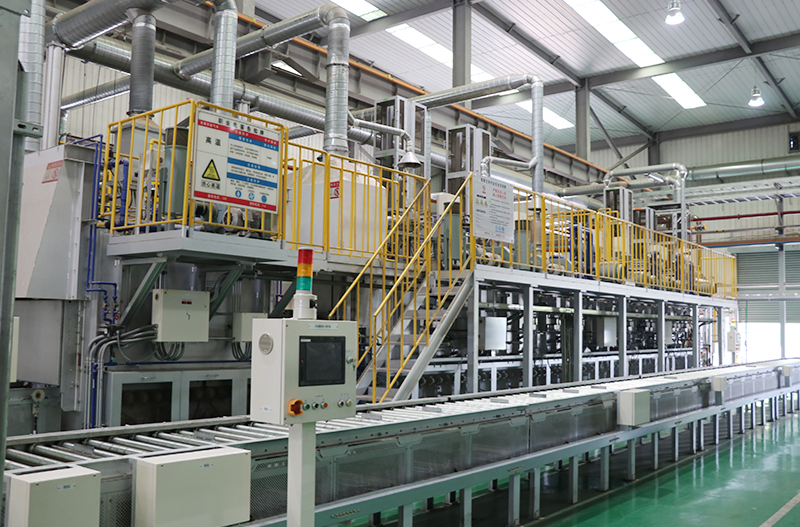
福建哪里有連續(xù)式滲碳爐銷售
實用配方與工藝,除灰工藝除了前述的硝酸和硫酸為基的工藝外,常常也用到含鉻酸、含磷酸、含氟化物的除灰工藝,這里不予分別說明,將收集的除灰工藝與配方列于下表中,處理后均需流動水清洗。表中工藝2用于壓鑄鋁,工藝用于高硅壓鑄鋁。產品Top Desmut S-10是非硝酸系除灰劑,通過添加硫酸而有強力除灰效果。Top Desmut N-10硝酸含量很低時就可特別有效地去除侵蝕后鋁材表面的掛灰。Top ADD-320原液使用,溫度≤40℃,時間15——60s,可均勻活化鑄鋁表面,清除污漬與掛灰。Top ADD-350 10——50g/L作用是恢復TopADD-320去污力。Top ADD-400 30mL/L可免除經過Top ADD-320處理后的材料在水洗中受到腐蝕。Specicalty 982是不含鉻的中和劑,適用于6000系列鋁;Specicalty 985則是不含鉻的中和劑,適用于2000系列鋁。
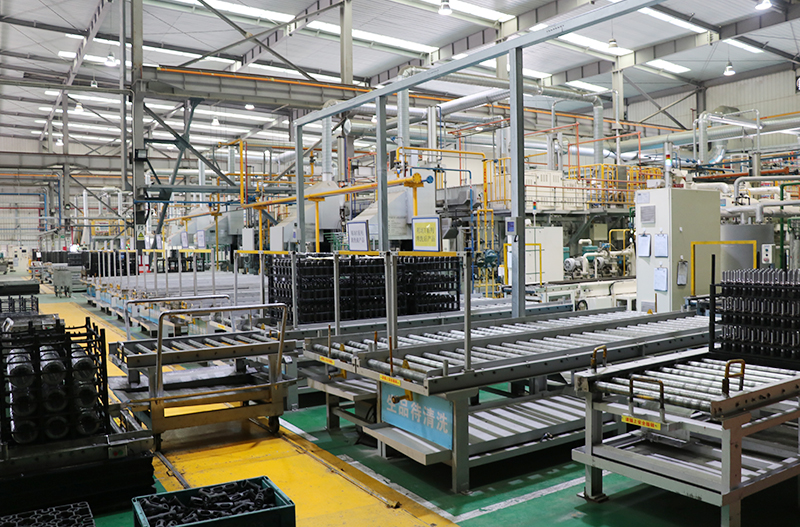
福建哪里有連續(xù)式滲碳爐銷售
碳氮共滲處理的特點及其與滲碳加工工藝的區(qū)別。碳氮共滲處理是在820~860℃溫度下,利用滲劑分解出的活性碳原子和氮原子,同時滲入工件表面的過程,共滲時間在1~3h,因此碳氮共滲具有滲碳和滲氮的雙重作用,共滲時間與滲層厚度、溫度和所用介質有關,共滲層的碳氮含量取決于共滲溫度。碳氮共滲處理的共滲溫度提高則碳含量提高,氮含量降低;共滲溫度降低則碳含量降低,氮含量提高,共滲層中碳含量在0.7%~1.0%,氮含量在0. 15%~0.5%,多用于低碳鋼、中碳鋼和合金鋼等,滲劑有固體、氣體和鹽浴三種。碳氮共滲后進行淬火+低溫回火處理,回火后的表層組織為含氮馬氏體+殘余奧氏體+少量碳氮化合物,心部為低碳馬氏體或中碳回火馬氏體。經過碳氮共滲處理,在確保工件內部高韌性的前提下,提高了表面硬度、耐磨性和疲勞強度,同時氮降低了奧氏體的形成溫度,故工件可在較低的溫度下實現共滲;且工件共滲后可直接淬火、不易出現過熱,工件的變形小;提高滲層的淬透性,可在緩和的介質中淬火處理;滲速快,作業(yè)周期短。

福建哪里有連續(xù)式滲碳爐銷售
介紹真空熱處理爐的用途特點與注意事項。真空熱處理爐的用途、特點與注意事項真空爐適用范圍:用于硬質合金、陶瓷、不銹鋼材料、粉末冶金、金屬注射成型,真空燒結脫蠟等實驗與工藝。具有大抽氣量、高真空度、溫度均勻可控和無泄漏等特點。1、溫度控制精度:±1℃2、升溫快、環(huán)保節(jié)能、精度高、性能穩(wěn)定、保溫效果好。3、脫脂,脫氣,燒結一體化處理爐內裝有密封箱,使脫脂揮發(fā)的氣體不污染內壁和隔熱材,全部排出到爐外。方形密封箱,使緊密型提高,可以對大量的成型濟,減少氣體及加熱電力消耗,降低運行成本。4、爐膛采用耐高溫硬碳氈,采用石墨棒加熱。5、內部加有循環(huán)水系統(tǒng),確保降溫速度加快。爐體溫度接近室溫,同時加有快速冷卻系統(tǒng)。6、可按用戶要求設計定制。1200℃小型真空熱處理爐和1400℃隔熱屏真空熱處理爐是兩種常見的熱處理爐。
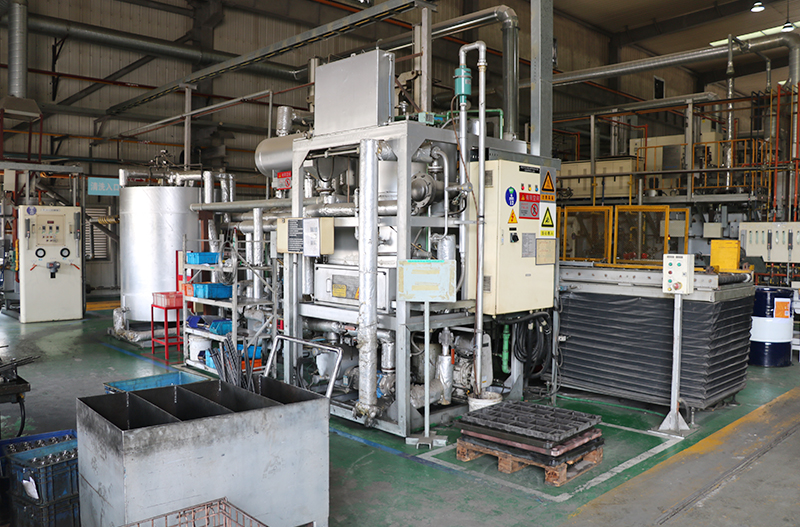
福建哪里有連續(xù)式滲碳爐銷售
能耗是比較大的,降能耗,提設備利用率,增加產品工藝快流通是降成本、提經濟效益的重要辦法,因此我們在設備固定化情況下工藝流程盡可能采用標準規(guī)劃、工藝文件等,并根據熱處理工藝節(jié)點的特點建立相應的工作規(guī)程,以減少不需要的損耗。建立工藝作業(yè)指導書,完善設備操作規(guī)程,要保熱處理工藝穩(wěn)定,同類材料同類技術要求的產品應編制相對應的作業(yè)指導書,流程細節(jié)化,指導書內容應包括裝爐量、裝料方式、主爐工藝參數設置、冷卻工藝、回火工藝、檢驗規(guī)程及卸料裝箱等。按照標準操作,就不會因為人員的變動因素而影響技術品質。建立交接班制度,一般情況下具有連續(xù)合作性生產的性質,需要員工有較高的協(xié)作精神和積極擔當的心態(tài)來完成每天當班的工作任務。以模具熱處理為例:清洗→裝料→淬火→回火→金相檢驗→清洗→送貨,完成整個加工過程要經歷多個班次,而每步的工作都會對下一道工序至后的技術品質有相關影響。